被誉为中国“核电粮仓”的中核建中核燃料元件有限公司(简称中核建中)坐落在万里长江第一城的宜宾,在这个亚洲最大的核燃料元件制造基地,有一群“干惊天动地事,做隐姓埋名人”的核工业人,他们以履行国家使命为己任,从事着被称为最强中国“核能芯”的核燃料元件制造工作。中核建中建厂54年来,一代代建中人践行“敬业报国、求精创新”的企业精神,发扬艰苦奋斗、自强不息的奉献精神,生产出中国核电站第一颗“粮食”,为中国核事业和核电发展壮大做出了不可磨灭的贡献,也成就了中国核电燃料元件制造的多项第一。
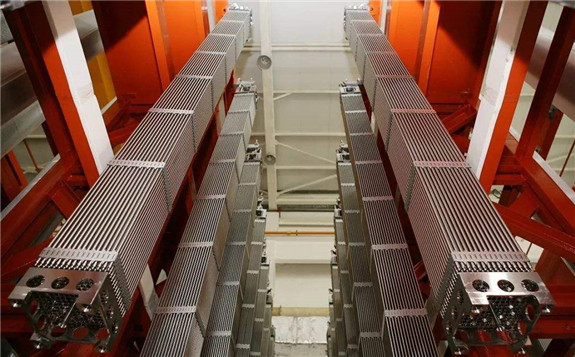
秦山核电燃料组件正式投产,成就中国核电元件制造第一
1989年12月初的一天,地处金沙江边的一间朴素且庄重的会议室里,聚集着中国核工业系统以及国务院三线办、核电办、能源部核总工办等部门的一百多位专家、学者和领导。
短暂的沉默。
人们在期待着什么?这是一代人、两代人甚至是三代人的期待!
幕然,一个两鬓已经斑白的老专家以他那低沉有力的话语打破了会场的寂静:“中核建中制造的秦山30万千瓦核电站燃料组件和相关组件符合设计要求,产品质量合格,同意验收出厂!”
这位老者,就是时任中国核工业总公司副总经理赵宏。当他将验收“合格证”郑重地颁发给时任工厂厂长时,会场内顿时响起了长时间热烈的掌声。
在上世纪80年代中期,回望掌声响起时的几年前,1986年中核建中随着中国核电建设起步,第一座秦山30万千瓦核电站“728”工程的上马,拉开了核电核燃料元件生产的序幕。
当时,对于从没有接触过核燃料元件生产的中国来说,所有的技术要重新学习研发,制造工艺从零开始,这无疑是个天大的难题。加上国家发展核电战略的调整,“728”工程建设经过了抢建、缓建、恢复建设这样一个较长的曲折之路。
当时中核建中核燃料元件生产线建设面临的问题十分棘手,外国专家到中核建中考察后说:“一天只有24小时,中国要在1988年制造出核燃料元件根本不可能。”
面对如此之大的困难,中核建中上下统一思想:“困难再大也得上!中国核燃料元件的研制,没有完不成任务的先例。泱泱大国,巍巍华夏,不能没有自己的核电,不能制造不出中国的核电元件……”。
为了争分夺秒抢建“728”工程核燃料元件生产线,中核建中全力以赴积极准备,把核电燃料元件工程建设放在中核建中工作的“重中之重”。中核建中组成多个攻关组,中核建中领导深入生产一线坐镇,对生产线的关键工艺进行技术攻关。当时的副总工程师刘芳言毅然决然地挑起了自主生产“728”元件三大零部件的攻关的领导工作。当时的三车间焊接工程师夏成烈(全国“三八”红旗手获得者)一人承担了多项预试验和合格性鉴定工作,为攻克上下管座焊接难关,她带领工人加班加点,反反复复进行了几十次试验,终于攻克了上下管座焊接技术难关。当时已是车间骨干的孙毓宝(原中核建中副总经理),和其他员工一样不服输,把八小时的工作制自觉地拉长到了极限。中核建中上下都是把办公地点搬到了核电燃料元件工程现场,从上到下,大家背水一战就为了一个不能更改的里程碑,按期生产出中国自己的核电燃料元件。
1991年12月15日,我国自行设计、自行建造的30万千瓦压水堆核电站秦山核电站并网发电,中国大陆无核电历史宣告结束。中核建中让外国专家口中的“不可能”变成了“可能”。
之后,凭借30万千瓦核燃料元件研发制造成功的实力,中核建中核燃料元件生产又创造了多个第一。
10000组燃料组件下线,成就中国核电元件产量、批量化生产第一
2015年5月6日,中核建中第10000组核电燃料组件在中核建中四车间顺利下线,中核建中成为亚洲压水堆核燃料元件产量和批量化生产最大的制造基地。
从1988到2015年,27年来,为了这10000组燃料组件,一批批中核建中人砥砺奋进、无私的奉献,创造了一个又一个奇迹。
2000年,为了实现中核建中高性能核燃料元件的国产化,时任车间主任的彭海青(现任中核建中副总经理、总工程师,全国“五一”劳动奖章获得者)和他的30人团队向含钆芯块燃料棒国产化发起了攻坚。他们充分利用现有资源,使用近3吨实验料,进行了50个批次的试验,用1年时间完成了国外2年时间才能完成的实验。2002年9月,他们的成果通过了法国专家监督下的产品合格性鉴定,从而进入规模化生产阶段,结束了高性能燃料组件使用的含钆燃料棒从国外进口的历史,也使中核建中成为世界上少数几个掌握这一技术的核燃料生产企业。
在2005年攻克全M 5AFA—3G技术难关的日子里,时任中核建中技术处技术科科长(现任中核建中科技部副主任)吴平和王刚等同志没日没夜地扑在全M5技术转让工作中,协调、组织全M5工艺预鉴定、鉴定及产品合格性鉴定,深入生产现场配合车间及时处理、解决发生的技术问题,保证了全M5技术转让各项工作始终按计划节点顺利推进。为制定管座最佳的加工方案,当时的三车间全国劳模、共产党员张世平调整流水孔加工顺序,经过多次试验,使全M5上、下管座加工时间比原来缩短了四分之一,且降低了管座生产成本,并一次性通过了管座产品合格性鉴定。
在2011年中核建中启动的新400吨扩建技改工程中,中核建中从上到下以“5+2”、“白+黑”的工作状态,争分夺秒,打响了“保安全、保质量、保进度、全员会战”战役攻坚战。仅用2年时间,于2013年底,建成中核建中核燃料元件新400吨生产线,产能达到800吨铀/年,中核建中跃升为全球为数不多具有较大规模的核燃料元件制造专业化公司,标志着中国压水堆核电燃料元件制造又跃上了一个新的台阶。
华龙一号全球首堆落地 成就华龙一号燃料元件制造第一
当前,中国已经成为世界制造业大国,突出优势是处于全球产业链中游,高铁、核电等一大批产业和装备处于国际先进水平,性价比好,符合很多国家需求和承接能力。”习近平总书记出访时多次推介中国制造。核电和高铁正成为中国技术“走出去”的两张亮丽名片。作为中国故事的“主讲人”,习近平总书记透过这些“国家名片”,让全世界看到一个活力盎然、和平友善、开放包容的中国。
华龙一号是中国在30余年核电科研、设计、制造、建设和运行的基础上,自主研发具有完整自主知识产权研发的第三代先进百万千瓦级压水堆核电机组。作为中国核电“走出去”的主打品牌,华龙一号全球首堆示范工程落户福清核电,中核建中光荣且自信地承担着华龙一号全球首堆福清5号机组核燃料元件的生产任务。
中核集团华龙一号燃料元件产业化技术研究重点科技专项实施以来,中核建中历经近9年的不懈努力,在各相关单位的紧密合作下,经历了原材料管控、工艺技术改进等多个阶段的技术攻关,成功掌握了华龙一号燃料元件批量化制造技术,且各项指标优良,填补了国内具有自主知识产权的大型核电燃料元件批量化制造的空白。
“每个项目都是硬骨头,但我们都按节点顺利完成。”中核建中华龙一号核燃料元件研制负责人说道。其上、下管座是燃料元件中的关键部件,管座的制造工艺非常复杂,尺寸精度要求极其严格。在华龙一号核燃料元件的科研以及生产过程中,通过对上、下管座图纸和技术条件的研究,从零部件机加工艺、上下管座组装操作方法、国产焊接材料的电子束和钎焊工艺设计、工装量规设计等角度不断优化工艺,最终顺利完成了生产研制任务。其中“管中管”胀接设备及工艺的成功研制,解决华龙一号核燃料元件重大科研项目的制造难题,确保华龙一号核燃料元件的顺利生产;进一步优化了格架外条带,具有良好的防钩挂性能;采用了“空间曲面”下管座设计,使元件具有了更好的防异物功能……这个有着各种类型压水堆核燃料元件生产经验的团队,构筑了铀化工、粉末冶金、零部件制造、组件组装焊接和检测等一系列华龙一号核燃料元件研制的核心技术,以比别人高的步频、比别人多的努力,在跟随、超越、引领的道路上砥砺前行。
“中核建中在半个多世纪的发展历程中取得了丰硕的成果,为国内外各大核电站提供了16000余组高质量的核燃料组件。我们一定要再接再厉,充分发挥好自身优势,要按照中核集团党组要求,全力保障华龙一号核燃料元件的研制任务圆满完成,向着建成国际一流核燃料元件制造基地的目标而不懈奋斗!”中核建中党委书记、董事长高海潮对自己这支敢干、能干的队伍充满信心,正胸有成竹地描绘着中核建中“十四五”乃至更长远的发展规划,为中国的核事业,为“核电梦”圆再立新功。
免责声明:本网转载自合作媒体、机构或其他网站的信息,登载此文出于传递更多信息之目的,并不意味着赞同其观点或证实其内容的真实性。本网所有信息仅供参考,不做交易和服务的根据。本网内容如有侵权或其它问题请及时告之,本网将及时修改或删除。凡以任何方式登录本网站或直接、间接使用本网站资料者,视为自愿接受本网站声明的约束。